The Pursuit of Comfort Daimatu’s Manufacturing
Daimatu, rooted in the tradition of crafting Suruga lacquered geta, remains committed to its passion to this day. We caught up with three legends to hear about their dedication first-hand.
Daimatu's Legendary Artisans
- Planning and Design Department Takahashi Kazuo
- After joining us in 1967 as part of the design department, Mr.Takahashi has played an active role in the planning and development of numerous products for our original brands.
- Technical Department Uchiyama Takashi
- After joining us in 1967, Mr.Uchiyama initially contributed to establishing overseas factories and providing technical guidance before transitioning to the technical department. There, he oversees the technical checks and grading for all our products.
- Manufacturing Department Ikegaya Kouichi
- After joining us in 1978, Mr.Ikegaya worked at our manufacturing plants in Shizuoka Prefecture, overseeing the production of various products. He has contributed to over 50 brands during his tenure.
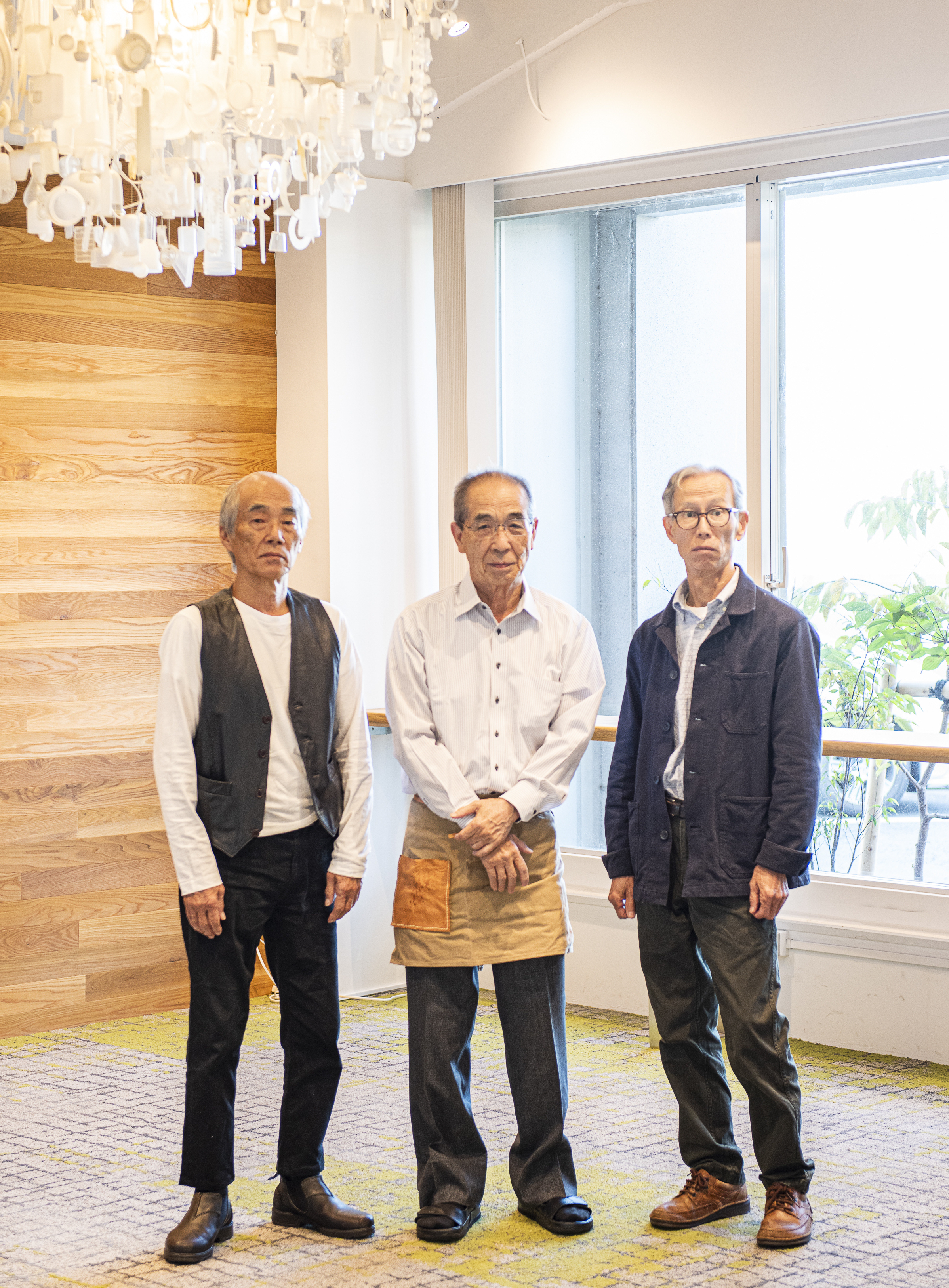
From left to right, Mr.Takahashi, Mr.Uchiyama, Mr.Ikegaya
Fashion trends change at a dizzying pace. Sandals are no exception.
Of the many sandals that now adorn shops throughout the year, what is Daimatu’s unique style?
The essence of Daimatu resides in the detail
In the design department, Mr.Takahashi defines the essence of Daimatu as ‘simple and gentle, visibly comfortable and lightweight, with a snug fit.’ It’s an answer that’s quite different from the trends of Paris or Milan, which are readily accessible to everyone in this age of instant availability.
So where does the focus lie for a legend? Mr.Takahashi explains, “Of course, we gather information from around the world.” He continues, “Using that information, we incorporate it into designs that are quintessentially Daimatu.”
What sets us apart? Compared to Westerners, Japanese people typically have slightly thicker feet by 3-4mm. They also tend to remove and put on their shoes more frequently. There’s a strong emphasis on uniformity in colour and pattern, as well as the texture of the material. While Tokyo experiences similar annual temperature variations to the dryer climates of Paris or Milan, except for winter, rainfall is nearly twice as much, particularly between June and August. Amidst this warm and humid climate, the unique sense of ‘comfort’ in footwear, nurtured by the familiarity with zori and geta sandals, remains unchanged for Japanese.
The essence of Daimatu lies in balancing trend awareness with a dedication to thoroughly meeting the needs of the user. The spirit of crafting practicality and style, as seen in the production of Suruga lacquered geta, runs deep.
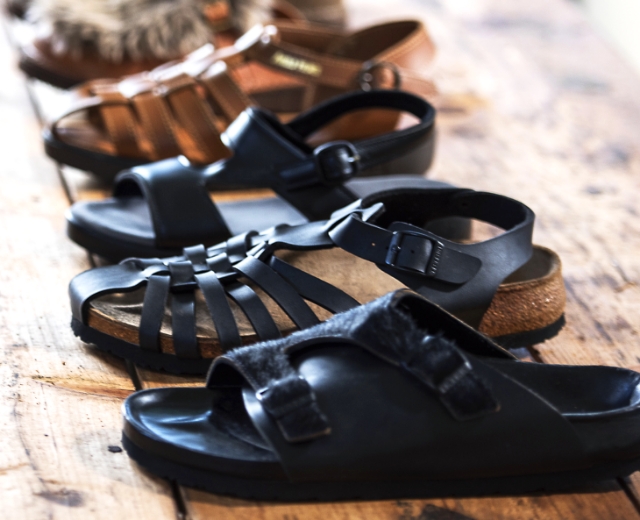
So, where does the essence of Daimatu manifest during the manufacturing stage?
“The Perfect Fit” : Sensory Satisfaction
“The role of the technical department is to adjust the lasts prepared by designers so that they can be manufactured in the factory,” explains Mr.Uchiyama. He prototypes and first checks for ‘comfort.’
If you find a pair of shoes you like in a store, you might try them on in front of a mirror and take a few steps to test them out. While it’s common to exchange for a different size or add insoles if they don’t fit right, Mr.Uchiyama’s perspective is different.
“Whether they’re too big or too small, anyone can tell. What we aim for is that feeling of the perfect fit. That’s why we check more precisely, making sure the shoes snugly fit, without rubbing against the ankles or Achilles tendon, and without feeling squeezed when stepping. If there are any issues, we adjust the lasts or patterns and retest them.”
Prototyping and testing are done meticulously and carefully. “If the fit isn’t right, no one will buy them,” Mr.Uchiyama explains.
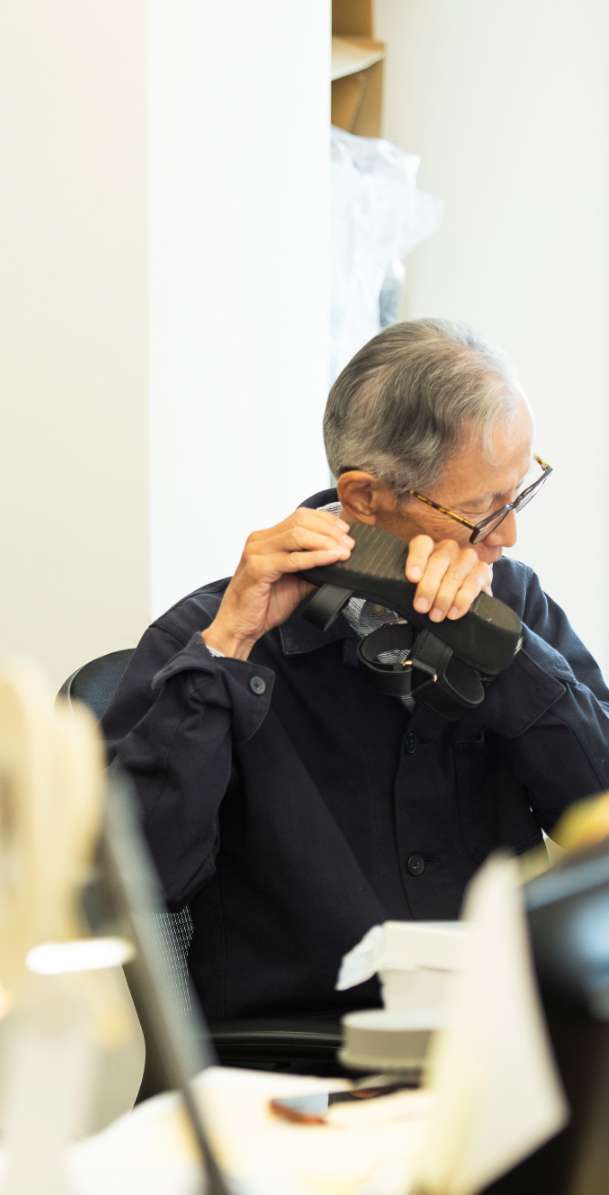
Daimatu is involved in a wide range of OEM and ODM collaborations, from renowned global brands to well-known domestic and private labels. Does the essence of Daimatu shine through in these ventures as well?
Taking on the world through OEM and ODM.

According to Mr.Ikegaya from the manufacturing department, the effort required for OEM and ODM support for overseas brands is incomparable to that of domestic products.
“Firstly, the moulds, machinery, and scale are different from our specifications. Some materials are imported, while others are sourced locally. Typically, adhesives are sourced domestically, so compatibility is unknown. Transportation methods and lead times vary greatly. Taking all of these factors into account, we establish a manufacturing plan. Once prototypes are produced, we confirm the finished quality and repeat this process until both parties are satisfied.”
Surprisingly, sandals with simple structures have many components. This leads to numerous areas to confirm in prototypes and increases communication.
What’s the reason for investing effort into OEM and ODM, even with these challenges?
“We see it as an opportunity to test how much we can improve and guarantee a certain level of quality. It’s about taking on the world.”
Mr.Ikegaya continues, “It’s not an exaggeration. We must not create unwearable products, and uncomfortable ones are also unacceptable. It’s all about making them comfortable to wear.”
The passion for seeking “comfort” knows no bounds.