Dedication to Comfort Daimatu’s Manufacturing
An insight into the process of achieving comfort
Processing materials to achieve a lightweight look
Sandals are made of a sole that supports the underside of the foot and a strap that holds the upper part of the foot. It’s remarkably simple. This simplicity underscores the emphasis Mr.Takahashi from the design department places on appearance. “The outsole’s appearance is where weight is most noticeable. Rubber soles often appear heavy, don’t they? The material texture influences the visual perception of ‘heavy/light’ like this.”
To address this, adjustments are made. Mr.Takahashi developed a sole with a honeycomb structure inside to reduce the amount of resin used, achieving physical lightness. While lightweight and comfortable outsoles like crepe or polyurethane are common, they degrade over time, potentially cracking due to hardening or hydrolysis. This is why we opt for rubber, ensuring it remains lightweight.
“When it comes to essential materials in design, we make sure to highlight their strengths while ensuring they feel light and comfortable when worn.”
The development focused on blending fashion and ease of wear supports the aspect of ‘comfort’.
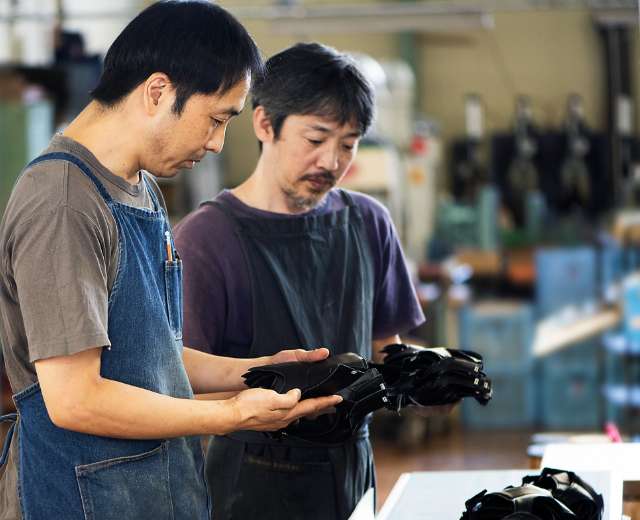
Coordination between departments to enhance shoe last design
“In the technical department,” Mr.Uchiyama explains, “our role is to negotiate and find solutions that respect both the designer’s vision and practical manufacturing requirements to finalise the mould.“
“If the seam allowance on the pattern is too small or the assembly appears impractical, we ask the designers to make adjustments. Conversely, if the process seems laborious, we propose more efficient methods to the manufacturing department.”
Mr.Uchiyama points out, “Occasionally, sandals may appear misshapen, resembling a koi fish’s mouth when viewed from the front.” He adds, “Even while walking around town, one might find their attention drawn to such sandals. This issue arises from incorrect positioning during the lasting process. With proper angles and positions, this problem can be avoided.”
“If the last hasn’t been checked for a proper fit, issues may arise later, necessitating adjustments by adding filler. In such cases, we may even manually correct the last.” Mr. Uchiyama explains that understanding which part of the sandal is assembled in each stage and machine, and how to perfectly match it to the last, allows for adjustments.
However, Mr.Uchiyama remarks, “It takes about 10 years to intuitively grasp this.”
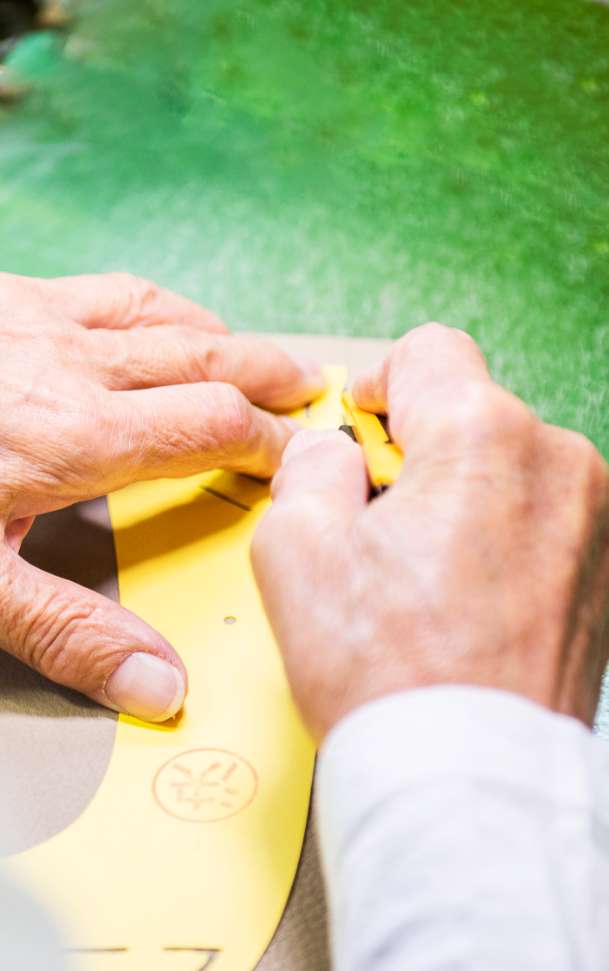
Smooth lasting is the key
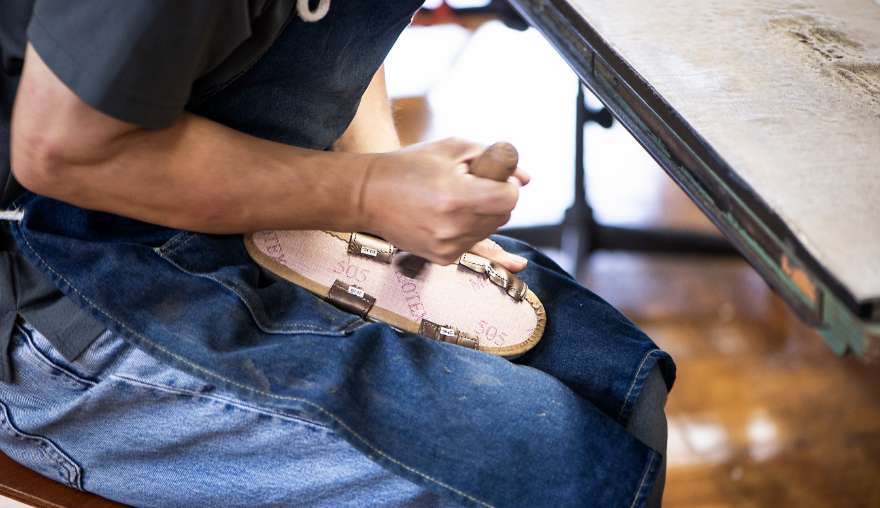
There is no guarantee that having a good last will lead to a comfortable sandal. It’s not as straightforward as that. Sandals present their own unique challenges. Unlike shoes, sandals often feature a shallow instep cutout. Depending on the design, any imperfections can be difficult to conceal.
Mr.Ikegaya from the manufacturing department explains, “It’s crucial to ensure the insole and upper match the last comfortably, without being too tight or loose, and in line with the last’s curvature. This is what determines comfort.” During the lasting process, the upper is carefully fitted over the last, aligned comfortably with its curvature, and then secured with adhesive to the insole. This step defines the shoe’s shape. Sandals typically feature thinner thread than regular shoes, requiring skilled handiwork during lasting.
Producing 300-400 pairs a day, workers may experience sore fingers. However, Mr.Ikegaya calmly asserts, “‘It’s the factory manager’s role to continuously encourage and support them.”
Daimatu, rooted in the tradition of crafting Suruga lacquered geta, remains committed to its passion to this day. We caught up with three legends to hear about their dedication first-hand.
Daimatu's Legendary Artisans
- Planning and Design Department Takahashi Kazuo
- After joining us in 1967 as part of the design department, Mr.Takahashi has played an active role in the planning and development of numerous products for our original brands.
- Technical Department Uchiyama Takashi
- After joining us in 1967, Mr.Uchiyama initially contributed to establishing overseas factories and providing technical guidance before transitioning to the technical department. There, he oversees the technical checks and grading for all our products.
- Manufacturing Department Ikegaya Kouichi
- After joining us in 1978, Mr.Ikegaya worked at our manufacturing plants in Shizuoka Prefecture, overseeing the production of various products. He has contributed to over 50 brands during his tenure.
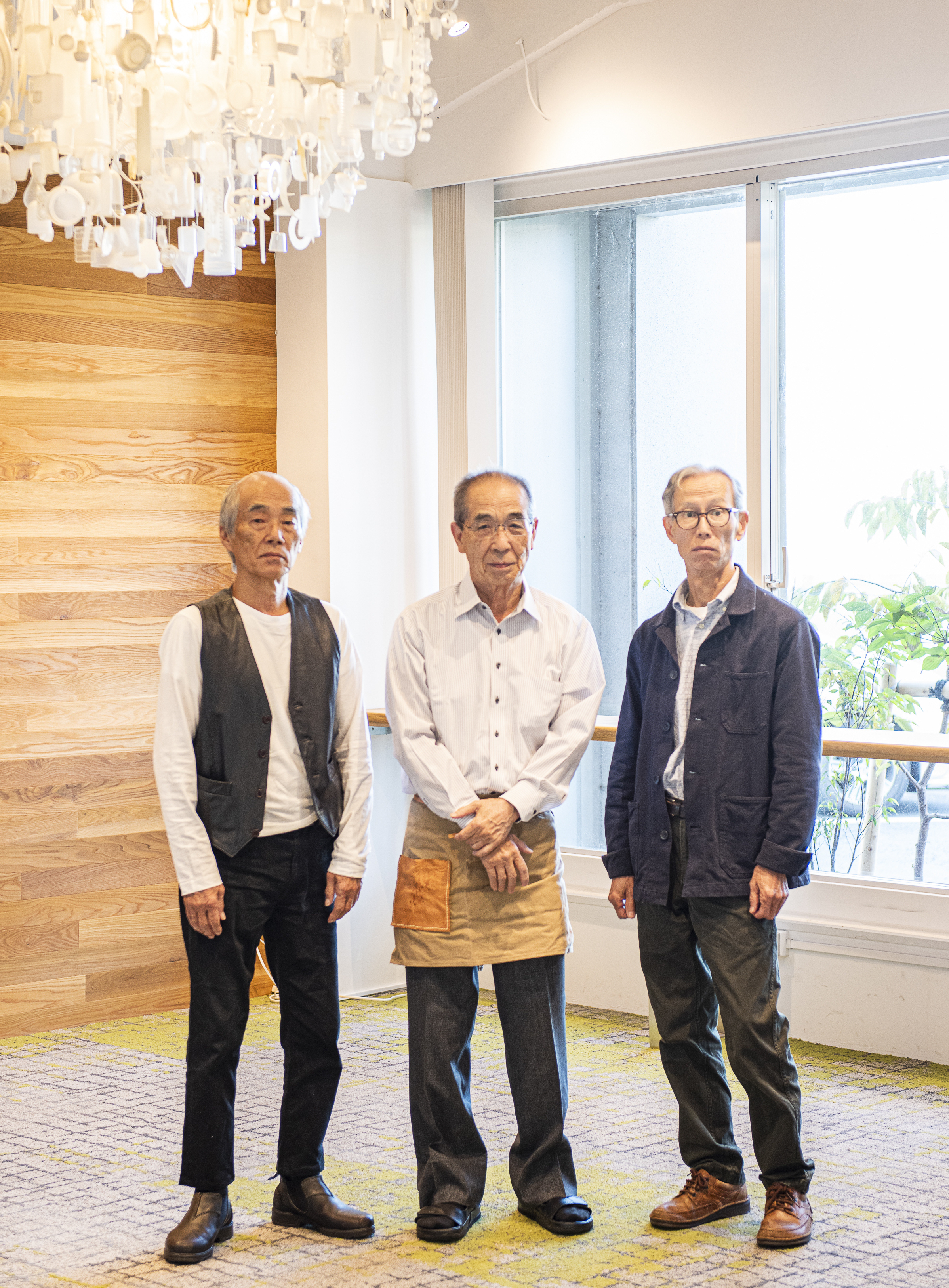
From left to right, Mr.Takahashi, Mr.Uchiyama, Mr.Ikegaya